Bonding WPS for Beginners: Getting Going with Welding Treatment Specs
Bonding WPS for Beginners: Getting Going with Welding Treatment Specs
Blog Article
Grasping Welding WPS Specifications: Finest Practices and Techniques for Quality Welds
In the realm of welding, mastering Welding Procedure Specification (WPS) criteria is an important part that straight influences the top quality and stability of welds. Abiding by these standards makes certain consistency and integrity in welding results. Nevertheless, achieving quality in welds exceeds simply understanding the criteria; it includes applying best techniques and strategies that raise the craft to a level of precision and ability that sets apart the average from the phenomenal. As we navigate with the intricacies of welding WPS criteria, discovering key insights and techniques for achieving top-tier welds will certainly be critical for welders looking for to stand out in their craft and produce welds that stand the test of time.
Recognizing Welding WPS Criteria

Inspectors count on WPS documentation to validate that welding procedures are being adhered to properly and that the resulting welds are of high quality. Designers use WPS standards to design welding treatments that guarantee the toughness and reliability of bonded structures.
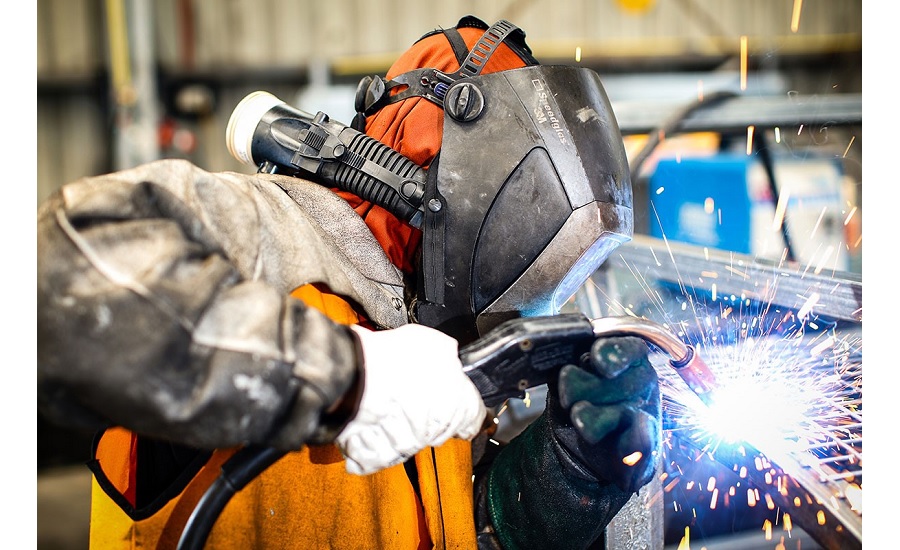

Vital Tools for High Quality Welds
Grasping welding WPS requirements is important for welders to effectively make use of the crucial tools required for producing top quality welds. The type of welding equipment required depends on the welding process being made use of, such as MIG, TIG, or stick welding. Cable brushes and chipping hammers are crucial for cleaning the weld joint before and after welding to remove any kind of contaminations that could influence the quality of the weld.
Trick Strategies for Welding Success
To attain welding success, one must understand the essential methods important for producing top notch welds. Maintaining a secure welding and a stable hand placement throughout the process is essential to achieving precision and uniformity in the welds. By mastering these essential strategies, welders can elevate the high quality of their work and accomplish welding success.
Ensuring Conformity With WPS Criteria
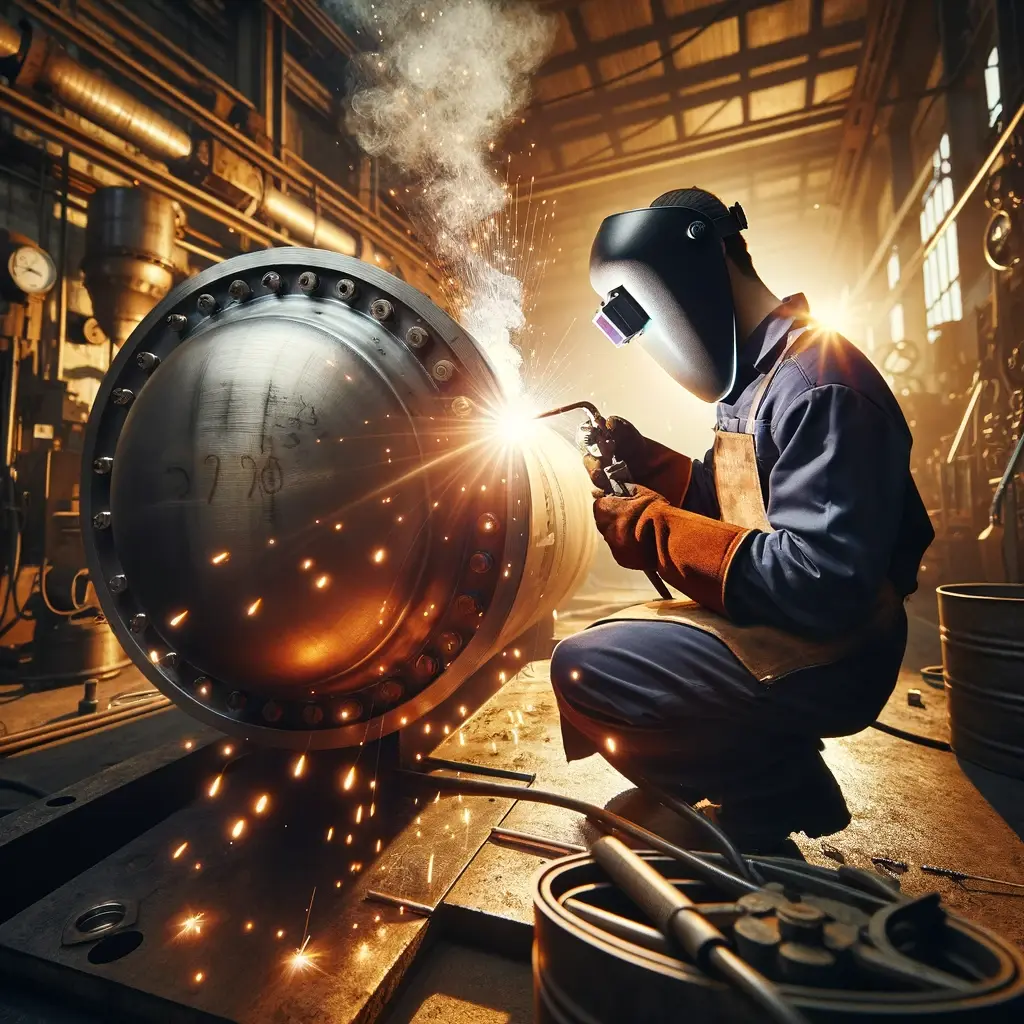
Additionally, welders should undergo training to familiarize themselves with the WPS standards relevant to their job. Routine audits and evaluations should be performed to verify that welding activities align with the prescribed WPS standards. Furthermore, maintaining comprehensive documents of welding criteria, devices calibration, and evaluation outcomes is critical for showing conformity with WPS requirements - welding WPS. By diligently sticking to WPS standards, welders can make certain that their work satisfies the necessary top quality degrees and adds to the overall success of the welding job.
Troubleshooting Common Welding Issues
When confronted with common welding issues, determining the origin cause is vital for effective troubleshooting. One common problem is the presence of porosity in welds, frequently triggered by contaminants such as oil, wetness, or rust. To resolve this, making certain appropriate cleansing of the base steel before welding and utilizing the appropriate securing gas can significantly reduce porosity. An additional problem often experienced is absence of fusion, where the weld stops working to appropriately bond with the base material. This can stem from inadequate warm input or inappropriate welding technique. Adjusting parameters such as voltage, wire feed speed, or take a trip rate can aid enhance fusion. Additionally, distortion, breaking, and spatter prevail welding challenges that can be minimized through appropriate joint prep work, regular warmth control, and choosing the ideal welding consumables. By completely recognizing these usual welding problems and their source, welders can successfully fix troubles and accomplish high-quality welds.
Verdict
Finally, understanding welding WPS criteria calls for a complete understanding of the standards, utilizing essential devices, and implementing key strategies for successful welds. view website Making certain conformity with WPS requirements is vital for producing top quality welds and staying clear of typical welding problems. By complying with best methods and methods, welders can accomplish regular and reputable cause their welding jobs.
In the realm of welding, grasping Welding Treatment Specification (WPS) requirements is an essential component that straight affects the quality and stability of welds.When diving right into the realm of welding methods, a critical aspect to comprehend is the relevance and details of Welding Treatment my review here Specification (WPS) requirements. WPS requirements give a detailed standard for welding operations, making sure consistency, quality, and safety and security in the welding procedure. The type of welding machine needed depends on the welding procedure being made use of, such as MIG, TIG, or stick welding.Achieving welding success with the proficiency of essential methods demands a thorough understanding and adherence to Welding Procedure Specification (WPS) requirements.
Report this page